Why industries should get critical components right for a resilient economy – Inside track
3 min read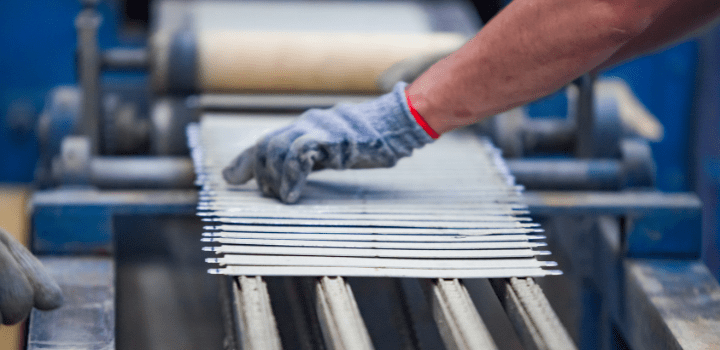
This post is by Dr Colin Church, chief executive of the Institute of Materials, Minerals & Mining and chair of Green Alliance’s Circular Economy Task Force. It is the third in our ‘Critical raw materials in focus’ series, a collection of blogs spotlighting the management of critical raw materials in the UK.
It has taken a while, but there is now an increasing understanding that we need to worry about the supply of certain ‘critical’ raw materials essential for maintaining our technologies and delivering the transition to a low carbon society.
One way to look at this is to consider how resilient our industries are to any shocks to those supply chains. In other words, are there mitigations in place that mean we can still install new electricity infrastructure, drive electric vehicles and check the latest ‘Strictly’ results on our smartphones, even if global or regional events have an impact?
To help understand this better, in 2023 an industry-led task and finish group examined the position of six key sectors: aerospace and defence; automotive; chemicals; electronics; energy; and medical technology. Its report identified the critical raw materials of most concern for each of those sectors, factoring in both supply and environmental, social, and governance (ESG) risks. It then suggested how, working together, industry and government could reduce vulnerabilities and increase resilience.
One major theme was the role a more circular economy could and should play. Being as efficient as possible and keeping the materials in high value use for as long as possible reduces the amount of new supply needed. This means more recycling as a minimum, but that can still be energy intensive and polluting. It can be hard when many critical raw materials are used in fairly small amounts in any given piece of kit (think rare earth magnets in an electric car, where they are maybe a quarter of a percent of the mass). Component or device reuse has more promise, but this requires design for disassembly and other, collective, actions on standards and interoperability.
The UK has advantages and big benefits to gainAlso important is to recognise the UK’s current advantages and build on them. Whether this is the strength of our research and innovation ecosystem, the historic legacy of mining and processing competence or the depth of our financial markets, these should all be leveraged more to support improving resilience.
A third aspect for greater resilience is the skills necessary for the better management of critical raw materials. As the 2023 IOM3 report The talent gap: critical skills for critical materials showed, the UK faces a real shortage in key skills across this value chain. Many of these jobs will be regional or local, thus supporting the economic development of different parts of the country, reaping a double benefit if we can get this right.
Finally, the study found there was real value to be had from a co-operative approach with government, both in developing a long term vision and in bringing in new policies or international partnerships, providing the context for industry to then act.
Participating in the industry group as its vice chair, something else really came through for me though. Whilst some sectors were doing significant work to understand their risks and work out how to manage them – diversifying suppliers, stockpiling, developing alternatives, etc – one or two seemed almost to have buried their heads in the sand. This is really worrying, and I would encourage any organisation in the six sectors we studied to take a look at the report and see what they can learn.
One final observation. The rhetoric is usually about critical raw materials. This is clearly important, you can’t make a lithium-ion battery without lithium. But in the end, what everyone wants is the battery, not the lithium. That doesn’t only require the materials that go into it, but also the facilities and the skills of the people to make it. Perhaps we need to start talking about ‘critical components’.
Colin Church was formerly vice chair of the Task & Finish Group on Industry Resilience for Critical Minerals.
Discover more from Inside track
Subscribe to get the latest posts sent to your email.