Vivobarefoot & Balena Take Next Step Toward Regenerative Barefootwear
3 min read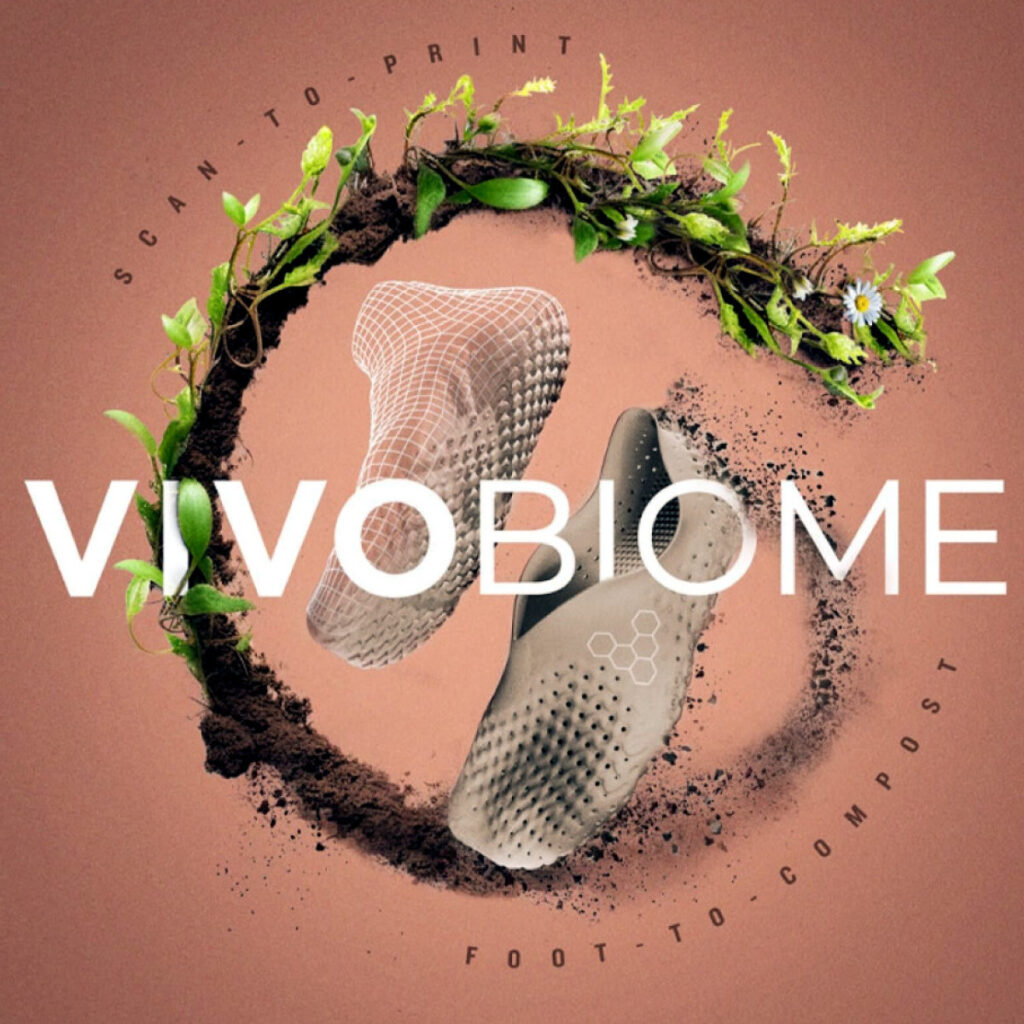
The footwear manufacturer and material-science company aim to deliver the
world’s first 3D-printed, made-to-measure footwear that is fully compostable.
Global natural health lifestyle brand
Vivobarefoot recently announced a partnership
with circular material-science startup
Balena — which developed its
biobased, compostable, recyclable, thermoplastic materials range
BioCir® for use in a variety of
industries. The partnership vision is footwear made-to-order, made-to-measure,
made locally, and made to be compostable and recyclable — an antidote to the
vast amounts of waste created by conventional shoe production.
Over-designed and over-produced, conventional shoes are now mass-consumed,
damaging to our
bodies,
and creating massive waste. In short, shoes are trashing our feet and our planet
— they make our feet weak; are made through off-shore, through often
less-than-ethical supply
chains;
and 12 billion pairs end up in
landfill every year.
The journey toward a circular end-of-life system for footwear faces a
significant challenge rooted in the intricate nature of shoes — both in their
design intricacy and the diverse materials used during manufacturing. The
complexity arises from the multitude of components — making recycling and
reintegrating used shoes into the supply chain a formidable task. Nike
recently unveiled its first fully circular shoe, designed for disassembly and
recyclability;
but industrywide efforts to change the wasteful ways shoes are made remain
piecemeal.
Vivobarefoot and Balena are hoping to prove that biodegradable material
alternatives and on-demand design and production offer a viable solution to the
challenges posed by the current limitations of recycling in the footwear
industry.
“The world doesn’t need new shoes. We need a new system and new materials,”
said Vivobarefoot co-founder Asher
Clark. “This future is
literally at our feet and this footwear will enable us to reconnect to nature,
move as nature intended and return footwear to nature when you’re done.”
Vivobarefoot acknowledges that it is part of the problem but also part of the
solution, thanks to initiatives such as
VivoBiome
— its scan-to-print, circular design platform that enables rapid prototyping to
save development and lab time, labor, and materials waste — revolutionizing the
shoe design and production process.
Now, Vivobarefoot aims to take this innovation a step further with the
incorporation of Balena’s BioCir flex
material — a compostable, biobased,
recyclable, thermoplastic material with advanced performance properties that
Balena developed for scaled durable goods production, including footwear, on a
mission to create a circular model for consumer industries.
Founded in 2020, Balena is on a mission to create a circular model for durable
consumer goods and solve one of the biggest challenges for achieving circular
models across industries: the products’ end-of-life. Founder David
Roubach
told Business Focus
he’s excited about the partnership with Vivobarefoot — which inspired the
creation of his own company.
“About 4 years ago, I heard Asher on stage with his amazing vision for
VivoBiome; and it was clear to me that in order to enable consumer product
companies to achieve true sustainability, there is a need to advocate for a
clearer circular economy model with a fundamental change in the materials we
use — and that’s what Balena is all about,” he said. “Seeing that collaboration become a
reality fills me with immense pride.”
BioCir flex maintains high flexibility, similar to TPU (thermoplastic
polyurethane — a standard filament for 3D printing), providing reliable and
long-lasting 3D-printed products. At the same time, it is biobased and
industrially compostable, reducing the environmental impact of discarded prints
— and for the first time, enabling 3D printing of flexible and durable items
while giving them the unique property of biodegradability, whereas traditional
TPU is non-biodegradable and contributes to plastic waste.
Prototypes are being made using a patented scan-to-print, computational design
system that, if scalable, will enable them to make bespoke, on-demand footwear
for individuals — not mass markets.
“Our goal at Vivobarefoot is to develop performance footwear that is both
durable and fully compostable,” Clark says. “This first-of-its-kind
collaboration moves us a step closer to that goal — giving us the ability to
make product design and development decisions based on science, which we’ve
never been able to do before.”